This article provides a technical analysis of boat deck foam flooring manufactured in China, addressing the common perception of inferior quality. It examines the factors that contribute to quality variations, including manufacturing processes, material science, and quality control standards. The review aims to provide an objective, data-driven perspective to help consumers and industry professionals differentiate between high-quality and low-quality products originating from Chinese manufacturers.
The Material Science of EVA Boat Deck Foam: A Global Standard
Regardless of origin, high-quality boat deck foam is typically made from Ethylene-Vinyl Acetate (EVA), a closed-cell copolymer. The performance characteristics of EVA foam are determined by its chemical composition and cellular structure. These key properties include:
- Water Resistance: The closed-cell nature of EVA foam prevents water absorption, mitigating mold, mildew, and material degradation. This is a critical factor in marine environments.
- Impact Absorption: EVA foam provides cushioning and reduces impact forces, enhancing comfort and safety on board.
- UV Stability: High-quality EVA foam incorporates UV inhibitors to resist degradation and color fading from prolonged sun exposure. Source: Society of Plastics Engineers
- Chemical Resistance: EVA foam generally exhibits good resistance to common marine chemicals, such as fuels, oils, and cleaning solutions.
- Non-Slip surface:The surface is usally made with brushed or embossed,to provide a non-slip surface.
These properties are not inherently linked to the country of origin. Rather, they are determined by the quality of raw materials and the manufacturing process.
Manufacturing Processes and Quality Control: The Key Differentiators
The manufacturing of EVA boat deck foam involves several crucial steps, each of which can significantly impact the final product's quality:
Raw Material Selection
The quality of the EVA resin, crosslinking agents, UV stabilizers, and pigments is paramount. Substandard materials will inevitably lead to inferior performance, regardless of where the foam is produced.
Foaming and Expansion
Precise control over temperature, pressure, and foaming agents is essential to achieve a uniform cell structure and density. This directly affects the foam's cushioning, water resistance, and overall durability.
Lamination and Adhesive Backing
Many high-quality boat deck foams feature a laminated top layer for increased wear resistance and a pressure-sensitive adhesive (PSA) backing for ease of installation. The quality and type of adhesive are critical for long-term adhesion to the boat's deck.
Surface Texturing
Many products are create with brushed or other surface.Like foam boat mat.
Quality Assurance
Reputable manufacturers implement rigorous quality control measures, including testing for:
- Density
- Tensile Strength
- Elongation
- UV Resistance (accelerated weathering tests)
- Adhesive Peel Strength
- Water Absorption
- Compression Set
Addressing the "Made in China" Stigma: A Reality Check
The perception that boat deck foam flooring made in China is inherently of poor quality is a generalization that doesn't reflect the reality of the manufacturing landscape. China's manufacturing sector is vast and diverse, encompassing both low-cost, low-quality producers and high-tech, internationally competitive manufacturers.
Identifying the Root Causes of Quality Issues
Problems associated with low-quality EVA boat deck foam, regardless of origin, often stem from:
- Inferior Raw Materials: Use of low-grade EVA resin, inadequate UV stabilizers, or poor-quality pigments.
- Inadequate Process Control: Lack of precision in the foaming, expansion, and lamination processes.
- Substandard Adhesive: Use of low-quality or inappropriate adhesives leading to delamination.
- Insufficient Quality Control: Lack of rigorous testing and inspection procedures.
These issues are not exclusive to Chinese manufacturers. They can occur anywhere if quality control is compromised.
The Rise of High-Quality Chinese Manufacturers
It's crucial to recognize that many Chinese manufacturers have invested heavily in advanced technology, quality control systems, and skilled labor. These companies are capable of producing EVA boat deck foam that meets or exceeds international standards. They often:
- Utilize state-of-the-art equipment.
- Employ rigorous quality control protocols (e.g., ISO 9001 certification).
- Source high-quality raw materials from reputable suppliers.
- Offer extensive testing data and certifications.
- Provide excellent customer support and warranties.
Comparative Analysis: High-Quality vs. Low-Quality EVA Foam
The table below provides a technical comparison of key quality indicators, highlighting the differences between high-quality and low-quality EVA boat deck foam. The origin is less important than these measurable characteristics:
Feature |
High-Quality EVA Foam |
Low-Quality EVA Foam |
Density (kg/m³) |
Typically 120-180 kg/m³ (depending on application and desired firmness) |
Often below 100 kg/m³, resulting in poor cushioning and durability |
Tensile Strength (MPa) |
> 0.5 MPa (indicating good resistance to tearing and stretching) |
< 0.3 MPa (prone to tearing and damage) |
Elongation at Break (%) |
> 150% (demonstrating good flexibility and resilience) |
< 100% (indicating brittleness and increased risk of cracking) |
UV Resistance |
Excellent; minimal color fade or degradation after prolonged UV exposure (e.g., >1000 hours in accelerated weathering tests, meeting ASTM standards) |
Poor; significant color fading and material degradation after relatively short exposure, indicating inadequate UV stabilization |
Adhesive Peel Strength |
Strong and durable bond to common marine substrates (e.g., fiberglass, aluminum), meeting or exceeding industry standards for marine adhesives |
Weak bond; prone to delamination, especially in wet or high-temperature conditions |
Water Absorption |
< 2% (by weight) after 24-hour immersion, indicating a well-formed closed-cell structure |
> 5% (by weight), indicating a poorly formed cell structure or damage, leading to waterlogging and potential mold growth |
Compression Set |
Low; retains its original thickness and cushioning properties after prolonged compression (e.g., < 10% compression set after 22 hours at 50% compression) |
High; loses significant thickness and cushioning properties after compression, indicating poor long-term performance |
Custom |
Wide range of custom colors and textures |
Limited design options, often basic |
Cost |
Higher upfront cost, lower long-term expense |
Low upfront cost, higher long-term repair costs |
Manufacturer Focus: Customization, Bulk Orders, and Quality Assurance
We are a Chinese manufacturer specializing in high-quality, custom EVA boat deck foam. We offer personalized designs, bulk and wholesale pricing, and a commitment to rigorous quality control. Our products undergo extensive testing to meet international marine standards. We utilize premium raw materials and advanced manufacturing processes to ensure durability, UV resistance, and long-term performance. Contact us for a quote and to discuss your specific needs. We are the supplier you can trust.
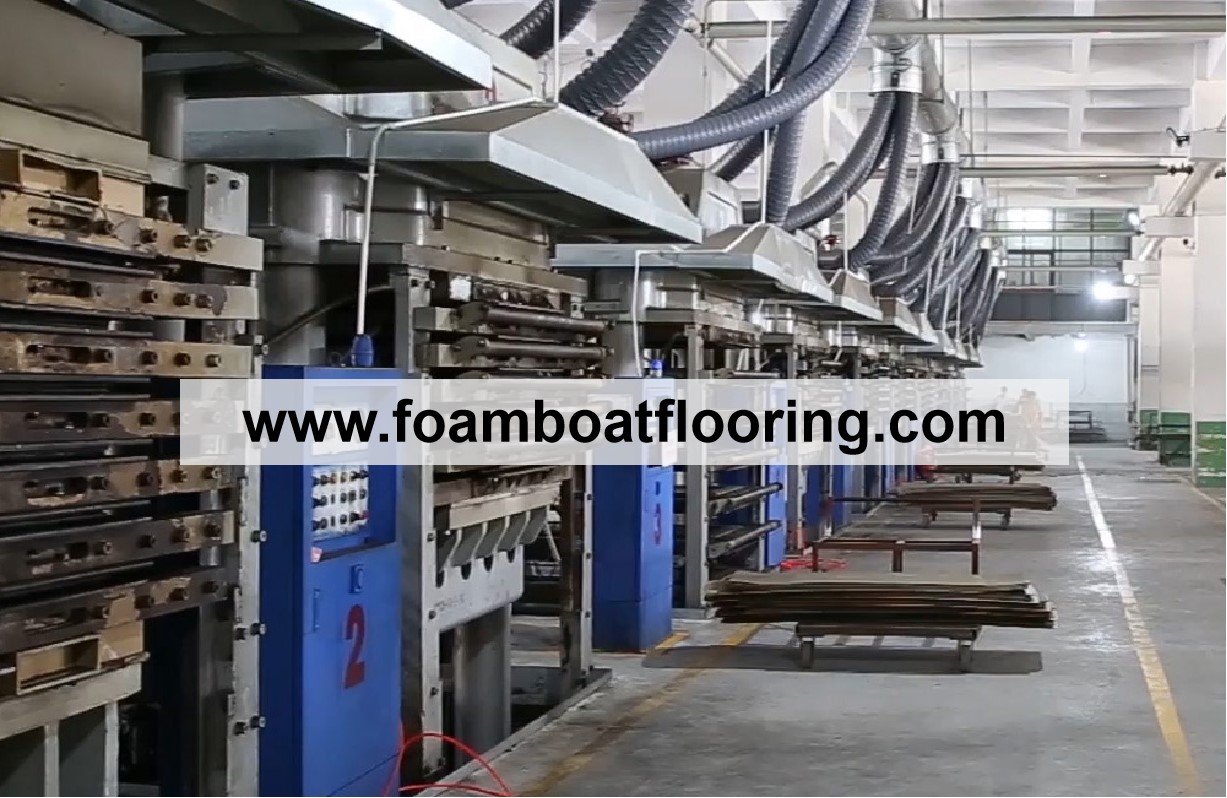
Frequently Asked Questions
What are the most reliable indicators of high-quality EVA boat deck foam?
Look for detailed technical specifications, including density, tensile strength, elongation, UV resistance data (hours of accelerated weathering), adhesive peel strength, and water absorption. Reputable manufacturers will readily provide this information.
How can I verify the claims of a Chinese manufacturer?
Request certifications (e.g., ISO 9001), testing reports from independent laboratories, and customer references. A reputable manufacturer will be transparent and willing to provide documentation.
Is it always cheaper to buy boat deck foam from China?
While Chinese manufacturers can offer competitive pricing, the lowest price should not be the primary deciding factor. Extremely low prices often indicate compromised quality.
What is the best way to install EVA boat deck foam?
Proper surface preparation is crucial. Ensure the deck is clean, dry, and free of any contaminants. Follow the manufacturer's instructions for adhesive application and installation.
How does the thickness of foam for boat floor affect performance?
The thickness of the foam for boat floor is crucial for comfort and shock absorption. Thicker foam provides more cushioning, which is beneficial in high-impact areas or for longer periods of standing. However, it's important to balance thickness with the overall design and weight considerations of the boat.
Can you tell if an eva foam sheet boat will perform well just by looking at it?
While a visual inspection can reveal obvious defects, it cannot fully determine long-term performance. Rely on technical specifications and testing data to assess quality.
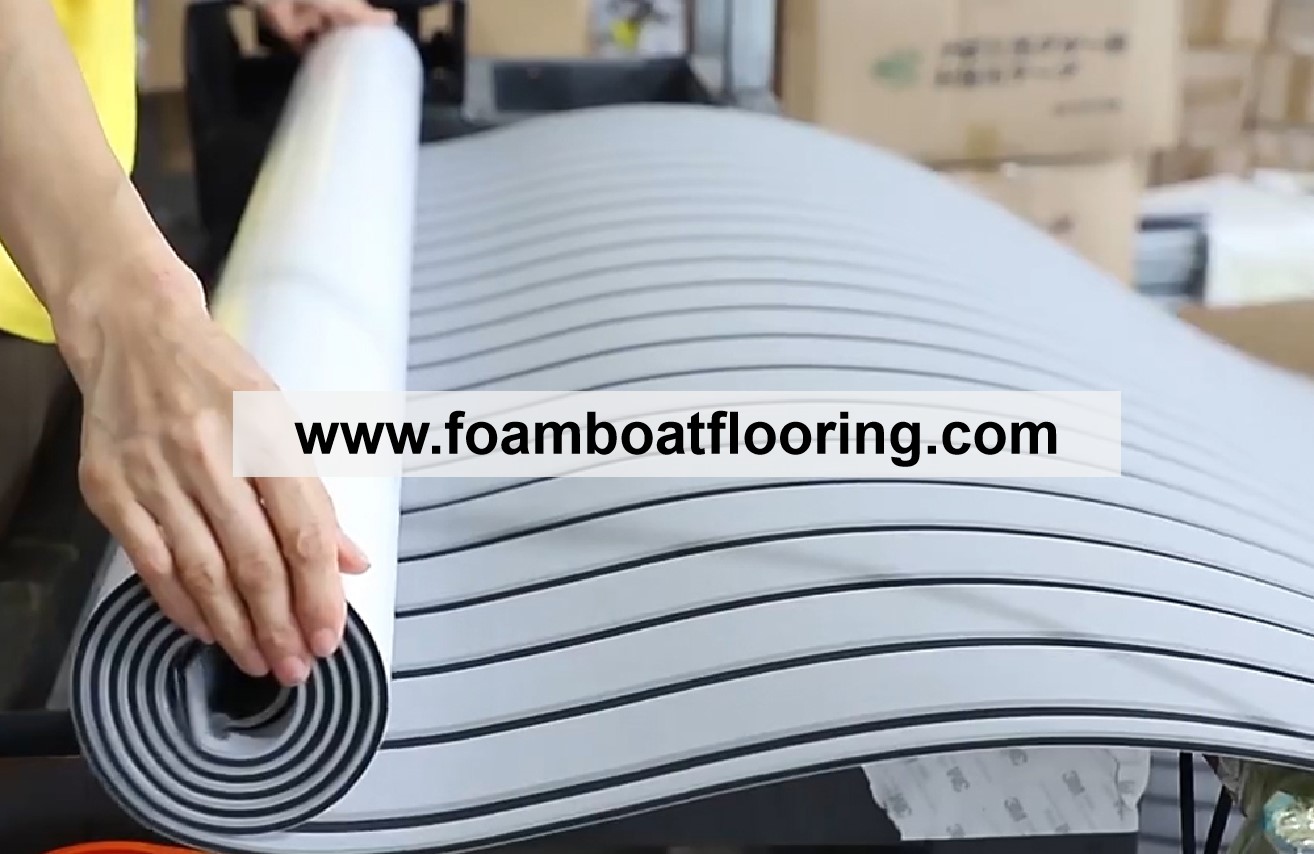
Key Takeaways
- The quality of EVA boat deck foam is determined by manufacturing processes and material quality, not solely by the country of origin.
- China has both low-quality and high-quality manufacturers of EVA boat deck foam.
- Thorough supplier vetting, including verification of technical specifications and testing data, is crucial.
- Focus on measurable performance characteristics rather than generalizations about "Made in China" products.
- Reputable Chinese manufacturers can provide high-quality, customizable, and cost-effective solutions.
- Consider Choosing a factory which can provide you with various option and solution .