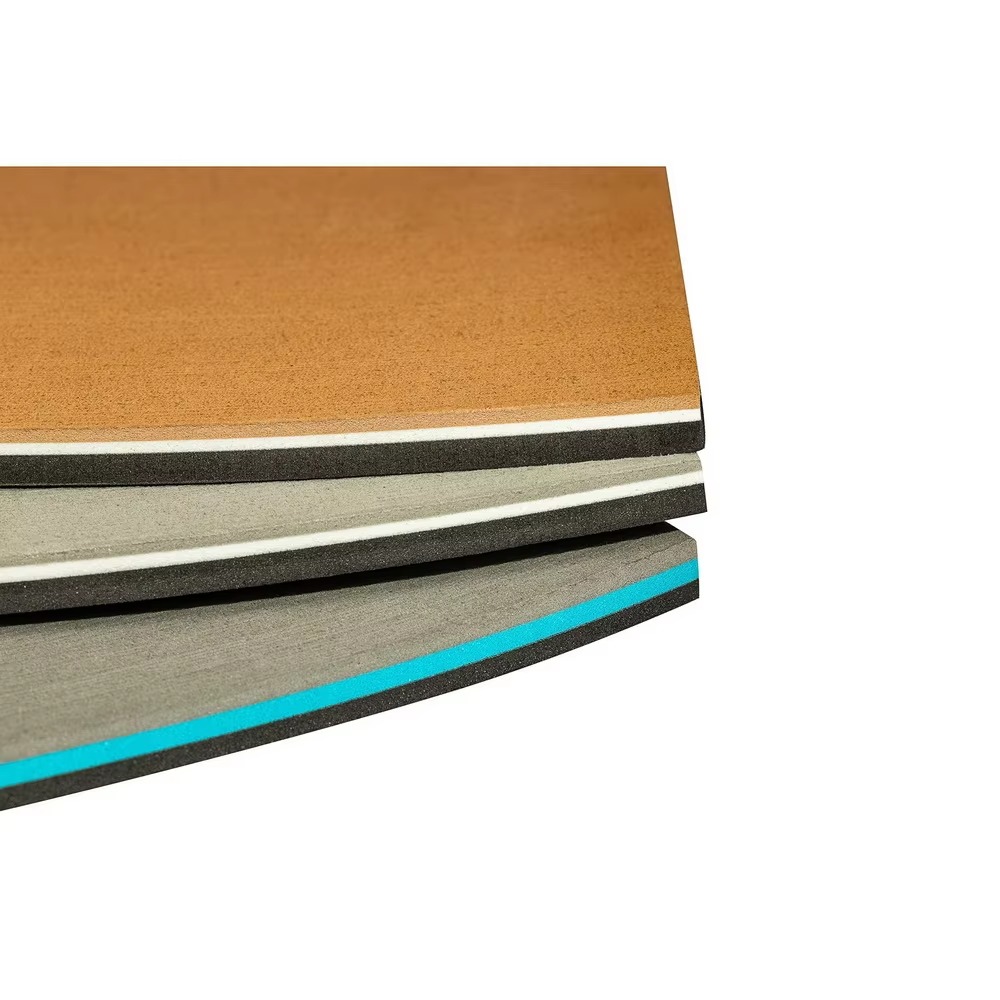
Lorem ipsum dolor sit amet, consectetur adipiscing elit, sed do eiusmod Lorem ipsum dolor sit amet consectetur adipiscing elit, sed do eiusmod lorem ipsum
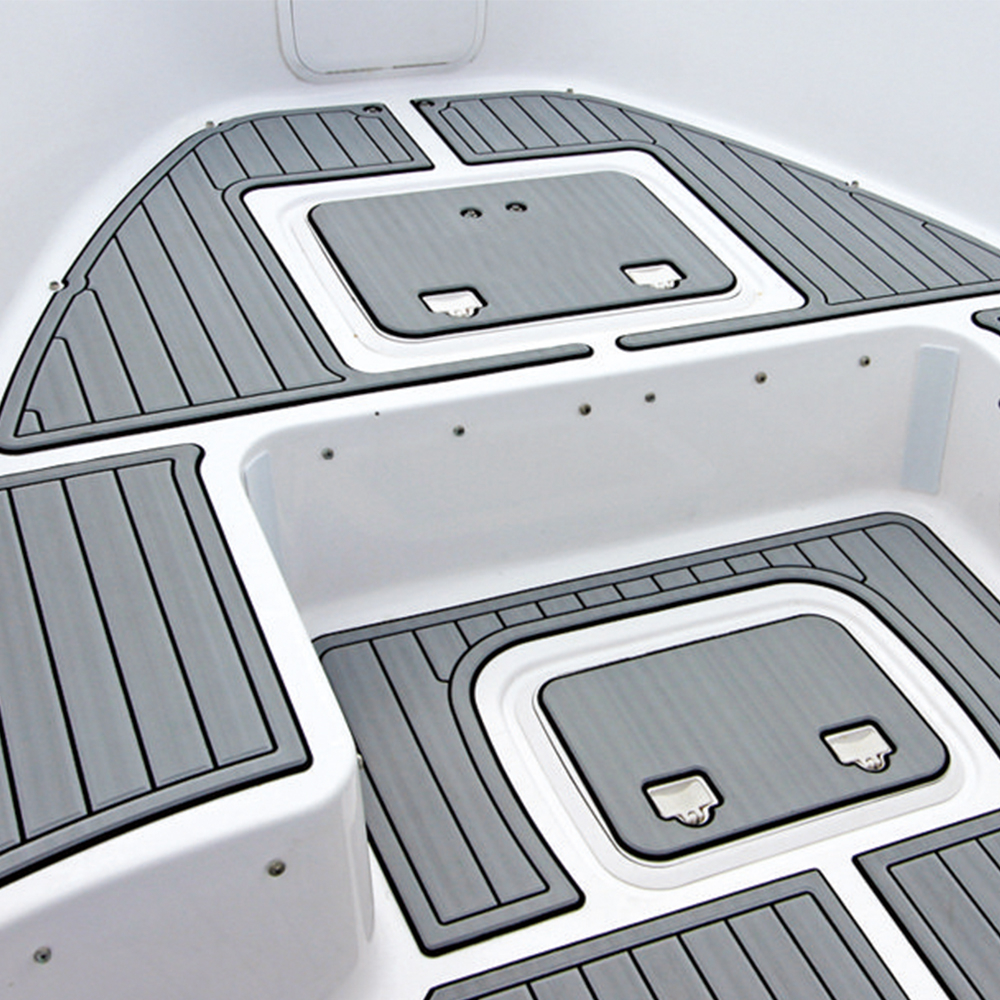
Applications of Boat Foam Pads for Enhanced Marine Performance
Boat foam pads, particularly those made from EVA (ethylene-vinyl acetate), are essential components in marine environments.
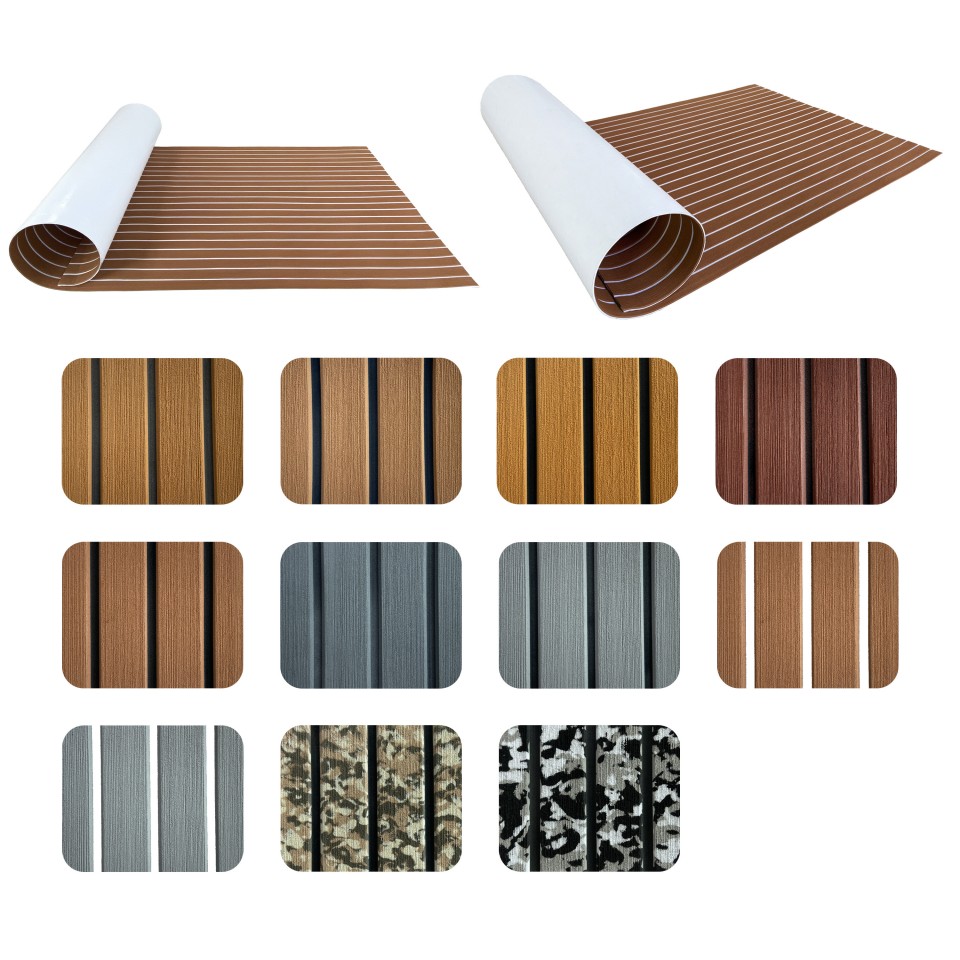
Boat Foam Decking Expert Advice on How to Remove and Replace Your Flooring
Boat foam decking is essential for maintaining both safety and aesthetics on private watercraft.
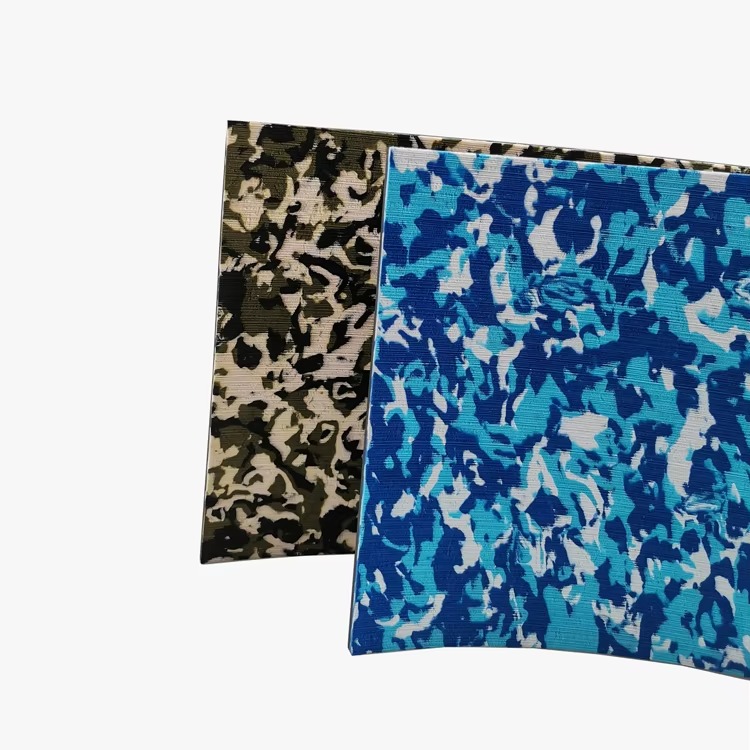
Bulk EVA Boat Closed Cell Foam
Home Table of Contents Product Specifications Material Marine Grade EVA (Closed-cell Foam) Hardness 50±5 Shore C Density 180Kgs/m3 Thickness 3mm,